讨论石墨电极的两种焙烧工艺
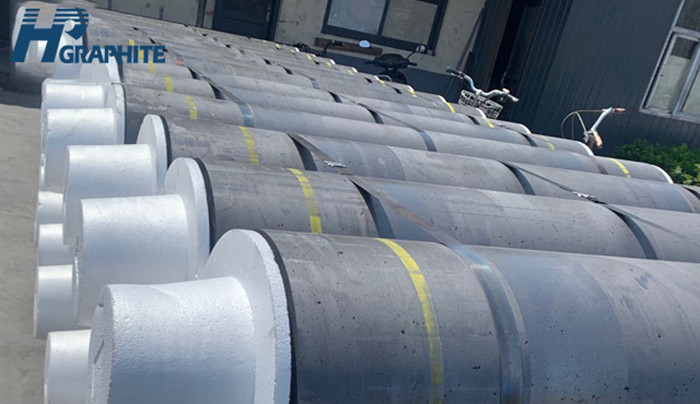
讨论石墨电极的两种焙烧工艺
1 产品的理化指标
环式炉焙烧的制品,其两端体积密度差异很大,MAX为0.048 g/cm3,平均在0.034 g/cm3左右,而车底炉在0.023 g/cm3以内。对于整支产品,环式炉焙烧的制品,无论是体积密度还是强度和电阻率在制品的两端都有显明差异,如图1。
两种工艺在加热时的温度场是不同的,车底炉为产品装在匣钵内,匣钵集中摆放在一个封闭的空间内进行加热(3个加热区),通过循环风机的搅动使炉内气氛温差保持在20℃以内。而环式炉是多个炉室连续运行组成的一个或几个火焰系统,一个炉室的几个料箱不仅在水平方向存在温差而且在垂直位置也存在较大温差,有的竟达到近250℃。 温差越大,制品的上下端升温速率差异越显明,往往超出制品的温升控制要求,致使产品的不均质性加重。对产品的实际测温显示,在关键温度250~450℃内,产品的上、下端温差车底炉在15℃以下, 而环式炉显明高于车底炉,达到6倍以上。同一支电极各部位升温速度的不同,会造成在焙烧过程中沥青的迁移、制品的体积膨胀和收缩的不同,造成焙 烧品的理化性能下降,且影响后工序石墨化的生产。
2 产品的内部质量
从制品上下端的中间钻取小样,发现环式炉焙 烧的小样往往在一端出现疏松、裂纹的情况,且平端后裂纹显明,如图2(a)、(c)。而车底式炉焙烧的电极,其上下端小样以及平端后外观致密,没有显著差异,如图2(b)、(d)。
生制品在焙烧过程中经历沥青软化、热解、聚合、成焦等阶段,相应地引起制品的膨胀和收缩,内部极易产生裂纹,这种裂纹即使浸渍也不能弥补。 生制品较差的导热率造成了制品外部先于内部固化,阻碍了挥发分的排除,使制品内部产生极高的应力。当电极的尺寸增大时,应平滑地减少关键温区的升温速率,延长焙烧曲线,如生产Φ800 mm超高功率石墨电极。
对于Φ600 mm及以上规格超高功率石墨电极,在内热串接石墨化生产时要经历3 000℃以上的高温,升温速度也很快,具有焙烧缺陷的制品经石墨化后缺陷会有不同程度的扩展,使制品的整体质量变坏,进而出现纵裂废品,而且这种产品在炼钢使用中也容易发生孔壁破裂、孔底折断或脱落。
3 结论与建议
1) 车底式焙烧炉优越的温度场可使制品在焙烧过程中按照设定的升温制度(制品温度)进行加热, 有利于制品径向和长度方向的质量均匀。而环式焙烧炉由于温差较大及炉内产品升温速率不一致,造成两端理化性能的显著差异,且制品内应力的增大,容易使制品产生裂纹缺陷。
2) 大规格超高功率石墨电极性能指标要求很高, 减小焙烧过程中制品的温差,可减少制品上下端质量的差异,提高石墨化成品率,减少炼钢应用中的孔壁折损事故。
3) 超高功率石墨电极制品在焙烧过程中,炭糊料和黏结剂沥青的热解缩聚行为存在很大差异,炭糊中针状焦对黏结剂沥青热解缩聚行为产生了重要影响,炭糊中针状焦改变了沥青的热解缩聚行为。建议在石墨电极生产中,针对不同的焙烧设备,进行炭糊的TGA测试,以制定关键温区的升温曲线。炭糊的TGA测试比黏结剂沥青的TGA测试更具代表性。
4) 对于大规格超高功率石墨电极的焙烧,车底炉工艺是极好的焙烧方式之一。延长焙烧曲线,可改善焙烧品的内部质量。
没有找到相关结果
0 个回复