矿热炉用挤压大规格Φ600~800mm石墨电极研制可行性分析
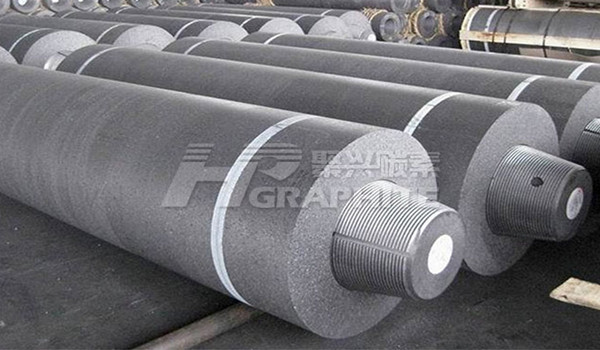
从技术层面、市场需求、节能环保等方面对研制挤压大规格Φ600~800mm高品质石墨电极(GHP)的可行性进行分析,并配套应用三相6根以及9根或12根电极供电布置在大容量矿热炉上冶炼新技术,改变矿热炉冶炼落后技术,有效发挥GHP 石墨电极优质特点,实现矿热炉大功率、大容量、节能减排、平安有效、低成本冶炼生产,为企业技术创新升级转型探索一条新的途径。
近几年,电石、铁合金、工业硅、黄磷、磨料等矿 热炉行业,因受环境保护、节能减排、平安、成本等方面影响,大部分企业经营不畅。目前,国内矿热炉行业冶炼技术水平同质化严重,经营较好的企业不是靠技术创新领导企业进步,而是靠优惠政策和资源优势维持生存和发展。国内大型电石、铁合金矿热炉还在沿用上世纪80年代从国外引进的采用炭素初级产品——自焙电极技术进行生产;工业硅行业冶炼还在向直径大于1200mm的振动成型炭电极和普通石墨电极上发展;黄磷冶炼行业尽管有所突破,但还在低质低价的普通石墨电极上打转;磨料冶炼行业也是采用低质低价的石墨电极,大部分是小容量冶炼。这种状况和发展趋势显然不符合“中国制造2025”我国战略对基础工业技术升级规划要求,这就要求矿热炉行业必须创新发展,实现整体突破,从而促进企业技术升级创新转型发展。河南科峰炭材料有限公司经过多年的探索和研究,整体分析矿热炉各行业生产技术特点,研制相适宜的挤压大规格Φ600~800mm高品质石墨电极(以下简称GHP电极),并配套开发一种新的冶炼技术,即在大型矿热炉上布置应用三相6根以及9根或12根GHP电极供电,同时优化冶炼运行技术条件,有效发挥GHP石墨电极结构好、强度高、导电佳、低灰分等优点,实现矿热炉行业大功率、大容量、节能减排、平安有效、低成本冶炼生产,彻底改变矿热炉冶炼技术落后现状,为企业技术创新升级转型探索一条新的途径,助力绿色经济良性循环发展。
1 挤压大规格高品质Φ600~800mm石墨电极适宜性分析
挤压大规格高品质Φ600~800mm石墨电极过去因挤压成型、石墨化、机加工装备、工艺技术、价格等因素影响,很少在20000kVA以上大型矿热炉上应用。现在我国35MN以上大型炭素挤压机有10台以上,大型LWG石墨化系统以及机加工系统使生产高品质Φ600~800mm石墨电极技术已不受限制。能够生产Φ600~800mmUHP石墨电极制造商均具有研制生产高品质GHP石墨电极的能力。若能在大型矿热炉上应用三相6根以及9根或12 根GHP电极供电,就可满足大容量40000kVA以上矿热炉生产。根据电石、铁合金、工业硅、黄磷、磨料等矿热炉不同炉况运行要求,研制指标适宜的挤压Φ600~800mmGHP石墨电极,相对其他冶炼导电电极其理化指标更优,直径合适,制造容易,性价比适宜。
1)性能指标优良
研制的挤压GHP石墨电极与国产G级炭电极、国外UCAR炭电极、矿热炉用振动成型石墨电极技术指标对比见表1。
从表1可以看到,挤压GHP石墨电极其理化技术指标优于其他电极。因大型压机可连续自动化挤压多根电极达到7~9t产品,产品会更均质,性能指标更优。若以优质针状焦作为挤压GHP石墨电极原料,则石墨电极的各向异性、高导电性、均质、高密高强、低灰分等性能可以满足不同冶炼客户的需求。
2)满足不同冶炼客户设计需求 一是可以针对性地研制电极本体抗折强度达到10~16MPa、接头抗折强度达到22MPa以上的GHP电极,相对于振动成型电极其高温下抗折断能力成倍增加,能有效减少因产品质量问题引起的停炉和责任事故几率。
二是可以选用低灰分的优质针状焦和黏结剂,研制灰分小于0.1%的石墨电极,使冶炼Si-2202以上牌号高品级工业硅变为可能。
三是可利用更先进的生产制造工艺,研制均质、高密、高强、抗 氧 化性石墨电极,体积密度大于1.73g/cm3,抗折强度大于12MPa。
四是可以选择优质原料,研制各向异性佳、高导电性、高导热性产品,电阻率小于5.5μΩ·m,能实现强化快速冶炼。
3)高品质挤压Φ600~800mm石墨电极针对矿热炉冶炼更适宜
目前矿热炉大部分采用三相交流电进行冶炼生产,冶炼采用大功率大电流生产时采用何种直径电极对单耗有极大的影响,这主要是由于集肤效应,这也是振动成型大直径导电电极设计电流密度一般小于10A/cm2的原因。当直径更大时,浸渍工序无法更好浸透,石墨化和焙烧周期更长导致成本上升,无法保证产品技术性能,故国内外石墨电极制造商的挤压产品MAX规格均为Φ800mm。
GHP石墨电极电阻率低、体积密度高、抗折强度高以及CTE低等优点,为设计大容量矿热炉提供了广阔的空间,可实现强化快速冶炼模式,可使每柱电极的通电电流>20A/cm2。
应用三相6根以及9根或12根Φ600~800mm GHP电极布局矿热炉供电冶炼,可以解决大容量矿热炉必须采用直径1200mm以上电极冶炼,特别是电石、铁合金等行业大容量冶炼采用此模式代替自焙电极后,综合成本减少30%变为可能,节能减排成效会更显明,环保治理更易实现,获取更多新闻内容可联系我们。
没有找到相关结果
0 个回复