技术|石墨制品石墨化裂纹原因分析Ⅰ
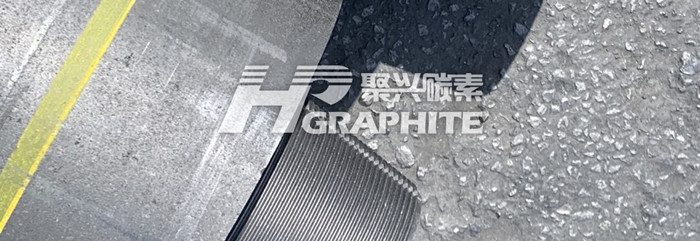
技术|石墨制品石墨化裂纹原因分析Ⅰ
石墨化是炭-石墨制品生产工艺过程中热处理的主要工序之一。艾奇逊石墨化炉是现行炭-石墨制品石墨化生产的主要炉型,是由装入炉内的制品与电阻料做“内热源”的直接加热间歇运转的一种特殊电阻炉,石墨化炉中装入制品和电阻料的空间被称为炉芯,炉芯截面积通常为3-6M2,向石墨化炉内通入强大的电流,借助于石墨化炉炉芯电阻,将电能转化为热能,使制品达到石墨化的温度Max值,完成石墨化过程,它遵循焦耳—楞茨定律。
由此可知,石墨化炉炉芯内不同点上的温度是不同的,而且在同一点,时间不同其温度也不相同,可见,石墨化炉炉芯温度既是空间的函数,也是时间的函数,从而炉芯内各部分的温度分布是不均衡的。
艾奇逊石墨化炉通电后,是依靠电阻料产生的热量来加热制品,使炉芯温度逐渐升高,炉芯各处的温度上升很不均匀,温度分布的差别很大,石墨化炉炉芯中部位置与炉芯两侧靠近保温料处的温度可相差数百摄氏度,炉芯上部与下部的温度差也可达百摄氏度。因此,同一石墨化炉炉芯内加热温度分布的不均匀是造成炉芯制品产生裂纹的主要 原因。
本人根据多年的石墨化生产经验,对于炭-石墨制品在石墨化生产过程中产生裂纹废品的原因进行了简要的总结和分析;在此和炭素工程技术人员共同探讨,以期达到减少炭-石墨制品石墨化生产工艺过程中的裂纹废品,提高石墨化工序的成品率,减少石墨化工序的生产成本,提高经济效益的目的。
制品石墨化裂纹原因
在石墨化过程中,制品产生裂纹的内在因素是制品的本体质量不高,抗热性能较差;外部因素是制品在石墨化过程中炉芯温度上升速度过快,制品上下或四周温度差也随之增大,热应力也相应增大是制品产生裂纹的主要原因。
1、石墨化工艺制度不合理
装炉方式
艾奇逊石墨化炉制品通常采用立装法装炉,立装法有正装和错装两种形式。炉芯制品正装时,对于任一根制品来说,只有一条高密度电流加热带,这一条加热带越宽,制品受热相对均匀一些,反之,受热很不均匀。错装时,每根制品存在两条高密度电流加热带,制品受热相对正装要均匀一些。因此,石墨化炉制品装炉方式选择不当,在石墨化送电过程中,制品周围温升速度相差较大,制品产生的热应力超出了本体能够承受的热应力,极容易使制品产生裂纹。
通电制度不合理
艾奇逊石墨化炉芯的温度变化曲线是采用定功率配电的功率曲线来控制的,如果石墨化炉通电制度不合理,确定的石墨化炉通电曲线开始功率过大和上升功率过快,使制品在通电过程中内外温度梯度过大,产生的热应力大大超过制品抵抗能力而产生裂纹。尤其是炉温在1300-1800度时,为严控炉温上升阶段,此阶段制品的物理结构和化学组 成开始发生很大变化,无定形炭的石墨化并未开始,实际上以化学反应为主,无定形炭微晶结构中结合的氢、氧、氮、硫等元素不断逸出,逸出的结果使无定形炭微晶结构边缘部分的杂质元素不断减少,并残留下若干晶格缺陷,同时促使热应力相对集中,极容易使制品产生裂纹。
电阻料的电阻
石墨化炉芯电阻是由制品的电阻与电阻料的电阻串联构成的,石墨化炉开始通电时电阻料的电阻约占炉芯电阻的99%左右,通电结束后电阻料的电阻还要占到97%左右,可见在整个石墨化过程中主要是电流通过电阻料产生的热量来加热制品,电阻料的电阻与制品的电阻相差较大时,在石墨化通电过程中,电阻料产生的热量远远大于制品本身的热量,造成制品内外温度相差过大,就会引起热应力过大使制品产生裂纹废品。
2、石墨化质量不高
装炉质量不高
石墨化装炉作业不符合工艺技术标准要求,装炉时炉芯制品排列不整齐,制品组间距不一致,电阻料填充不均匀,还有出现电阻料 “膨料”现象,这样就会出现在石墨化炉送电过程中炉芯各处的电流分布很不均匀,导致制品加热和温升速度很不均匀,制品内部温差过大,产生的热应力使制品产生裂纹废品。
电阻料质量不均匀
石墨化装炉采用混合焦做电阻料时,由于冶金焦的电阻率比石墨化焦大5-8倍,如果冶金焦和石墨化焦混合不均匀,炉芯各处的电阻分布很不均匀,造成通电时炉芯各部位的温升速度很不均匀,制品上下和四周温差过大,热应力也随之增大,容易使制品产生大批量的裂纹废品。
石墨化炉炉芯偏流
根据艾奇逊石墨化炉电热规律可知,石墨化炉芯内的温度分布,不仅与炉芯电阻有关系,而且也与炉芯中通过的电流大小有密切关系。当艾奇逊石墨化炉炉芯由于各种原因出现偏流情况时,炉芯各处通过的电流大不相同,炉芯温度的分布差别很大。当炉芯电流分布相差较大时,电流大的部位产生的热量多,该区域的制品温升较快,电流小的部 位产生的热量少,该区域的制品温升较慢,因此炉芯温度分布相差较大,从而制品内部温差也大,产生的热应力也相应增大,使制品产生裂纹废品。
3、焙烧品本体质量
焙烧品内部裂纹
有资料介绍,制品在焙烧过程中 350-500度和700度及其以上的温度区间是炭材料有可能发生破坏的尤其危险的温度范围。当制品的外表面温度为800度,MAX径向温差为10.7度时,半径50-65mm的区域决定材料的强度状况,在毛坯中部半径65mm的范围内,形成了危险的拉应力区。当温度为700度或更高时,该区域的应力远远大于材料的断裂强度的极值,这就是制品产生纵向平直裂纹的原因,这种裂纹一般不会扩展到制品的外表面,即制品的内部裂纹。
制品的均质性
炭-石墨制品密度分布的均匀性,制品的径向密度与轴向密度分布的均匀性高低与制品石墨化热处理过程中质量好坏密切相关。制品密度分布不均匀处,在石墨化热处理过程中,由于热应力的作用,制品容易产生内应力,相应地制品内应力的分布也不均匀,这种不均匀的内应力容易使制品产生裂纹,从而造成石墨化过程中出现裂纹废品。
制品体积密度偏高
炭-石墨制品的体积密度主要随生产原料、工艺技术条件的不同而变化,制品的抗折强度、弹性模量、热导率随体积密度的增加而增大。当体积密度偏高时,制品的弹性模量增加,脆性增大,导致制品的抗热冲击性能较差,在石墨化热处理过程中,由于高温产生的热应力大大超出了制品本身能够承受的应力,内外应力相差较大,制品产生裂纹废品。
前工序生产不稳定
由于石墨化是炭-石墨制品生产末尾的一个热处理过程,也是温度(Max)的一个热处理过程。一般认为,当前工序生产不稳定或出现质量波动时,在石墨化过程中会集中暴露出来。如果煅烧料温度低,沥青软化点不合格,焙烧温度低,浸渍增重率不合格等,制品在石墨化高温处理时,会造成二次收缩,或收缩不均匀,相当容易产生裂纹废品。
气胀现象
制品石墨化过程中产生某种程度的不可逆体积膨胀,其主要原因是制品在石墨化过程中,由于硫分集中急剧逸出而引起的,这种不可逆膨胀的程度随着含硫量的增加和热处理速度的加快而增加,这种不可逆膨胀行为被称为“气胀现象”。
众所周知,经过1350温度煅烧处理后的石油焦,非碳元素如氢、氧、氮等的含量一般低于0.1%;但是,硫和芳香烃的碳原子结合得相当牢固,以致于c—-s键在1400度以上才开始断裂,生成硫和硫碳化合物;在更高的温度下,主要是在1500-1800度时,所生成的硫和硫碳化合物以气体的形式急剧地从制品中释放出来,对制品产生很大的内应力,在制品内形成微小的孔洞和裂纹,当硫分含量达到一定的程度时,往往会导致石 墨化过程中的制品产生裂纹,联系我们获得更多技术资讯。
没有找到相关结果
0 个回复